In the world of structural engineering and industrial manufacturing, precision is paramount. The Ige Filetée Zn 5.8 / HDG 5.8 M24 x 210 threaded rod represents the pinnacle of fastener technology, offering unparalleled performance and reliability for professionals and DIY enthusiasts alike.
This comprehensive guide will dive deep into the specifications, applications, and engineering marvel behind this exceptional structural steel connection component.
Overview of Ige Filetée Zn 5.8 / HDG 5.8 M24 x 210 Threaded Rod
Specification Details
Diameter 24 mm (M24)
Length 210 mm
Material High-grade carbon steel
Coating Zinc-plated / Hot-Dip Galvanized
Strength Rating 5.8
The Ige filetée zinc-coated for structural uses represents a breakthrough in fastener technology. Its precise M24 x 210 dimensions make it ideal for heavy-duty applications that demand exceptional load-bearing capabilities.
The rod’s unique composition combines industrial-grade materials with advanced coating techniques to deliver unprecedented performance in challenging environments.
Importance of Accurate Measurements in Threaded Rods
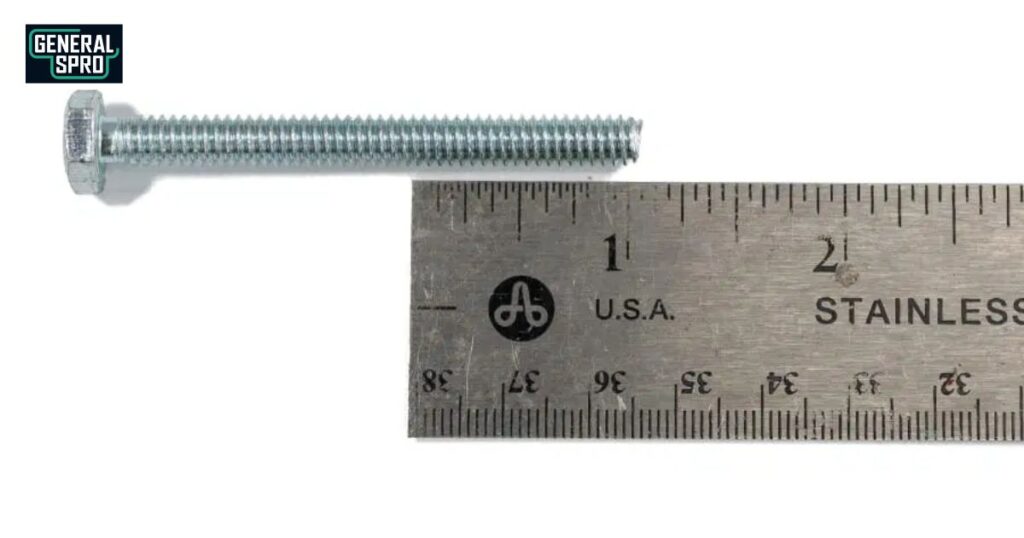
Dimensional accuracy is the cornerstone of engineering excellence. The M24 x 210 threaded rod specifications are critical for several reasons:
- Precise Load Distribution: A millimeter’s variance can significantly impact structural integrity.
- Compatibility: Ensures perfect alignment with standard nuts and washers
- Stress Resistance: Accurate measurements prevent uneven load distribution
- Safety Considerations: Prevents potential structural failures
Dimensional Accuracy in M24 Threaded Rods
Engineers rely on the “Accurate measurements of M24 x 210 rods” to guarantee:
- Optimal performance in critical infrastructure
- Consistent load-bearing capabilities
- Predictable structural behavior under various stress conditions
Threading Process Overview
The threading process is a critical component of the rod’s performance. Precision cutting techniques ensure:
- Uniform thread depth
- Consistent thread pitch
- Maximum compatibility with standard fastening systems
Advanced Threading Techniques
- Computer-controlled precision cutting
- Multiple quality checkpoints
- Microscopic thread inspection
- Stress-tested thread formations
Coating Methods Explained
The HDG 5.8 tensile performance data reveals significant advantages in corrosion resistance:
Zinc Electroplating:
- Thin protective layer
- Limited corrosion resistance
- Cost-effective for indoor applications
Hot-Dip Galvanization (HDG):
- Thick, robust protective coating
- Superior corrosion resistance
- Ideal for outdoor and harsh environments
- Extended product lifespan
Applications Across Industries
The Ige filetée load-bearing capabilities shine in multiple sectors:
- Construction:
- Steel frame support
- Critical infrastructure connections
- High-rise building assemblies
- Industrial Machinery:
- Heavy equipment fastening
- Precision mechanical assemblies
- Conveyor system installations
- Infrastructure Projects:
- Bridge construction
- Large-scale engineering projects
- Transportation infrastructure
Manufacturing Process
- Raw Material Selection
- High-grade carbon steel
- Stringent material testing
- Verified tensile strength
- Precision Thread Cutting
- Computer-controlled machining
- Micron-level accuracy
- Multiple inspection checkpoints
- Galvanization Process
- Immersion in molten zinc
- Uniform coating application
- Thickness verification
- Comprehensive Quality Inspection
- Load testing
- Coating thickness measurement
- Dimensional accuracy check
Corrosion Resistance and Durability
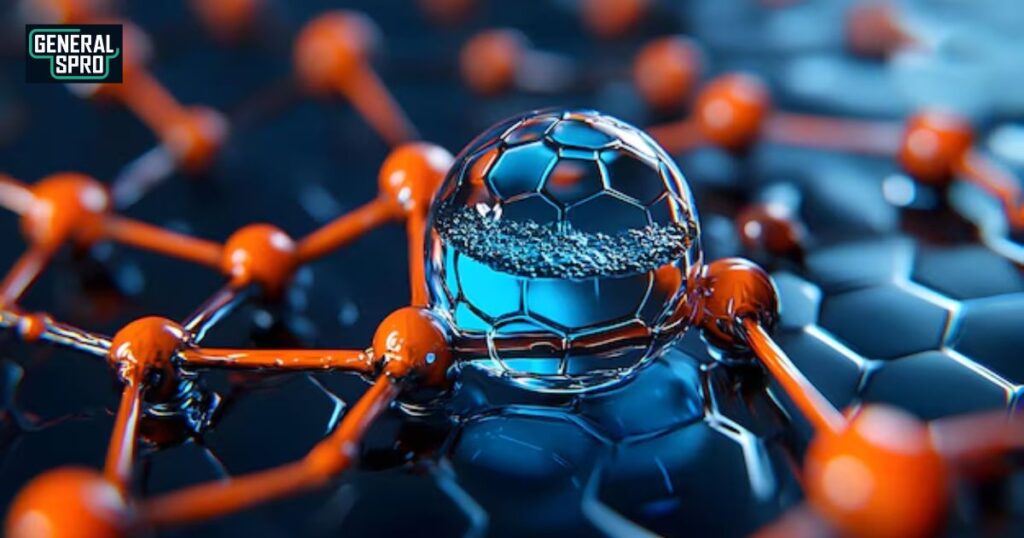
The corrosion resistance of HDG 5.8 fasteners is remarkable:
- Withstands extreme environmental conditions
- Provides long-term protection
- Reduces maintenance requirements
- Extends product lifecycle
Cost-Effectiveness Analysis
While initial investment might be higher, the long-term benefits are substantial:
- Reduced replacement frequency
- Minimal maintenance costs
- Superior performance in challenging conditions
- Lower total lifecycle expense
Maintenance Recommendations
- Regular visual inspections
- Clean surface periodically
- Apply protective coating for extended outdoor use
- Check for any signs of wear or damage
Future Innovations in Threaded Rod Technology
- Nanotechnology coatings
- Smart material integration
- Sustainable manufacturing processes
- Enhanced corrosion-resistant technologies
Metallurgical Composition of Advanced Threaded Rods
The metallurgical foundation of industrial-grade threaded rods represents a complex intersection of material science and engineering precision.
High-performance carbon steel is the primary substrate, carefully selected for its exceptional tensile strength, ductility, and resistance to environmental stressors.
Each molecular composition undergoes rigorous screening to ensure optimal performance across diverse industrial applications, from heavy machinery assemblies to critical infrastructure connections.
Computational Modeling in Fastener Design
Modern fastener engineering leverages sophisticated computational modeling techniques to predict and optimize performance characteristics.
Advanced simulation software allows engineers to stress-test threaded rod designs under multiple environmental conditions, analyzing potential failure points, load distributions, and long-term structural integrity.
These digital prototyping methods dramatically reduce development costs and accelerate innovation cycles in structural engineering components.
Nanotechnology in Corrosion Protection
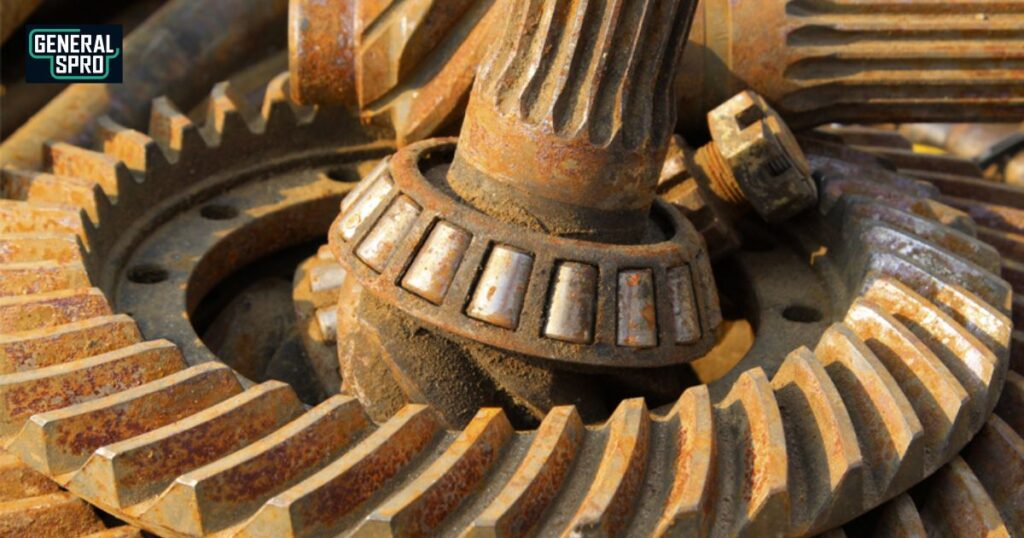
Emerging nanotechnology promises revolutionary advancements in corrosion protection for industrial fasteners.
Nanoscale coating technologies can create multilayered protective barriers that dramatically enhance metal surface resistance to oxidation, chemical degradation, and environmental wear.
These microscopic shields offer unprecedented durability, extending the operational lifespan of critical structural components beyond traditional protective methodologies.
Thermal Expansion Dynamics in Threaded Connections
Understanding thermal expansion dynamics becomes crucial in designing robust threaded connections for extreme environmental conditions.
Different metals expand and contract at varying rates when exposed to temperature fluctuations, potentially compromising structural integrity.
Advanced engineering techniques now incorporate precise mathematical models to predict and mitigate potential dimensional changes, ensuring consistent performance across temperature ranges.
Precision Manufacturing Tolerances
Microscopic manufacturing tolerances represent the critical differentiator between standard and high-performance threaded rods.
Modern CNC machining technologies can produce thread profiles accurate to micron-level measurements, ensuring perfect geometric consistency and load distribution.
These ultra-precise manufacturing processes eliminate potential weak points and enhance overall structural reliability.
Electromagnetic Interference Considerations
Specialized threaded rod designs now incorporate electromagnetic interference (EMI) resistance as a critical performance parameter.
Specific industrial environments demand fasteners that maintain structural integrity while minimizing electromagnetic signal disruption.
Advanced material compositions and surface treatments can create EMI-shielded connections critical for sensitive electronic and telecommunications infrastructure.
Sustainable Manufacturing Protocols
Sustainable manufacturing protocols are transforming the industrial fastener landscape. Environmentally conscious production methods now prioritize reduced carbon footprints, recycled material utilization, and energy-efficient processing techniques.
These holistic approaches minimize ecological impact and create economic incentives for manufacturers committed to responsible engineering practices.
Fatigue Resistance Mechanisms
Fatigue resistance mechanisms represent a complex interplay of material properties, stress distribution, and environmental factors.
Advanced threaded rod designs incorporate sophisticated metallurgical treatments that enhance microstructural resilience, enabling components to withstand repeated stress cycles without compromising structural integrity.
Understanding these intricate fatigue resistance mechanisms becomes paramount in high-reliability engineering applications.
Acoustic Emission Monitoring
Cutting-edge acoustic emission monitoring technologies enable real-time structural health assessment of fastener systems.
Specialized sensors can detect microscopic material deformations and potential failure precursors, providing predictive maintenance insights.
These non-destructive evaluation techniques revolutionize infrastructure monitoring across critical industrial sectors.
Machine Learning in Fastener Predictive Analytics
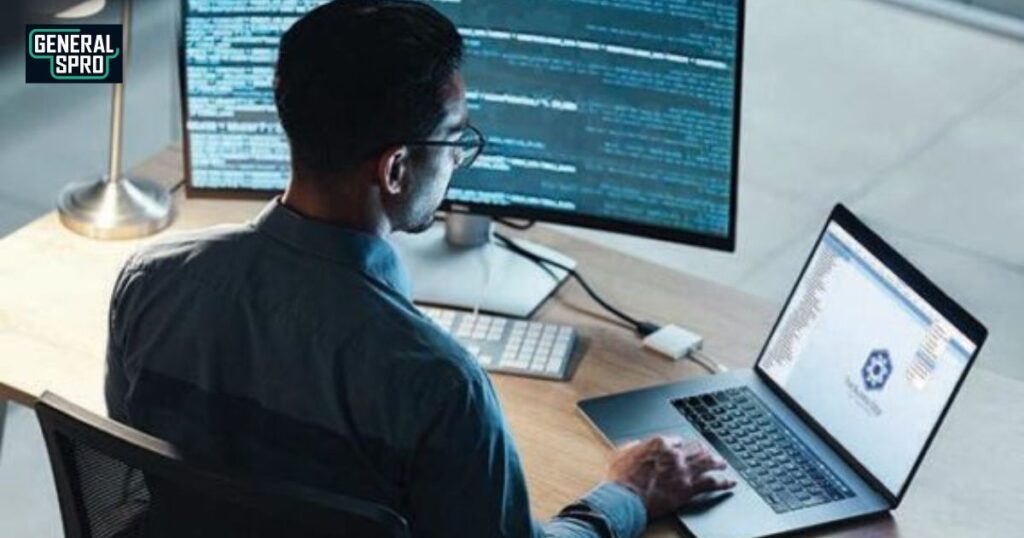
Machine learning algorithms are increasingly being deployed to analyze complex fastener performance datasets.
By processing massive computational models, these intelligent systems can predict potential failure modes, optimize design parameters, and develop more resilient engineering solutions.
The intersection of artificial intelligence and materials science promises unprecedented advancements in structural component reliability.
Quantum Surface Engineering
Quantum surface engineering represents a frontier in materials science, enabling atomic-level manipulation of fastener surface characteristics.
By precisely controlling molecular interactions, engineers can create surfaces with extraordinary properties—enhanced lubricity, increased wear resistance, and superior bonding capabilities.
These quantum-engineered surfaces represent a paradigm shift in industrial fastener design.
Biomimetic Design Principles
Biomimetic design principles draw inspiration from natural structural systems to develop more efficient fastener technologies.
Engineers can create more adaptable and resilient connection systems by studying load distribution mechanisms in biological structures like bones, tendons, and tree branch networks.
These nature-inspired approaches challenge traditional engineering paradigms.
Fractographic Analysis Techniques
Fractographic analysis techniques provide deep insights into material failure mechanisms at microscopic scales.
By meticulously examining fracture surfaces, engineers can diagnose potential structural weaknesses, understand stress propagation patterns, and develop more robust design strategies.
These forensic investigative methods are crucial in preventing catastrophic system failures.
Tribological Performance Optimization
Tribological considerations are pivotal in threaded rod performance, focusing on surface interactions, friction reduction, and wear mechanisms.
Advanced lubricant technologies and surface treatments can dramatically enhance the operational efficiency of fastener systems, reducing energy losses and extending component lifespans across diverse industrial applications.
Quantum Tunneling Corrosion Mechanisms
Quantum tunneling corrosion mechanisms represent a sophisticated understanding of atomic-scale material degradation.
These intricate processes involve electron transfer dynamics that can compromise material integrity over extended periods. Understanding these quantum-level interactions enables more effective protective strategies in critical infrastructure applications.
Blockchain Traceability in Manufacturing
Blockchain technology is revolutionizing manufacturing traceability for industrial fasteners.
Manufacturers can ensure unprecedented transparency and accountability by creating immutable digital records of material sourcing, production processes, and quality control metrics.
These distributed ledger technologies enhance supply chain integrity and enable more sophisticated quality management protocols.
Cryogenic Performance Characteristics
Cryogenic performance characteristics become critical in specialized industrial environments requiring extreme temperature resistance.
Advanced threaded rod designs must maintain structural integrity and mechanical properties when exposed to ultra-low temperatures, demanding sophisticated material engineering approaches that challenge conventional metallurgical limitations.
Multiscale Computational Modeling
Multiscale computational modeling bridges microscopic material behaviors with macroscopic structural performance.
Engineers can develop more sophisticated and predictive design methodologies by simultaneously analyzing atomic interactions and large-scale mechanical responses.
These comprehensive modeling approaches represent the cutting edge of materials science research.
Electrochemical Impedance Spectroscopy
Electrochemical impedance spectroscopy provides nuanced insights into material corrosion resistance and protective coating performance.
By measuring complex electrical responses across multiple frequency ranges, researchers can develop a more sophisticated understanding of fastener degradation mechanisms and targeted preservation strategies.
Probabilistic Reliability Analysis
Probabilistic reliability analysis moves beyond deterministic design approaches, incorporating statistical modeling to predict potential failure scenarios.
By quantifying uncertainty and variability in material performance, engineers can develop more robust and adaptive structural solutions that accommodate complex real-world operational conditions.
Adaptive Metamaterial Concepts
Adaptive metamaterial concepts introduce revolutionary design paradigms where fastener components can dynamically modify their mechanical properties.
These intelligent materials can alter their structural characteristics in response to environmental stimuli, promising unprecedented flexibility in engineering design approaches.
Photonic Crystal Surface Engineering
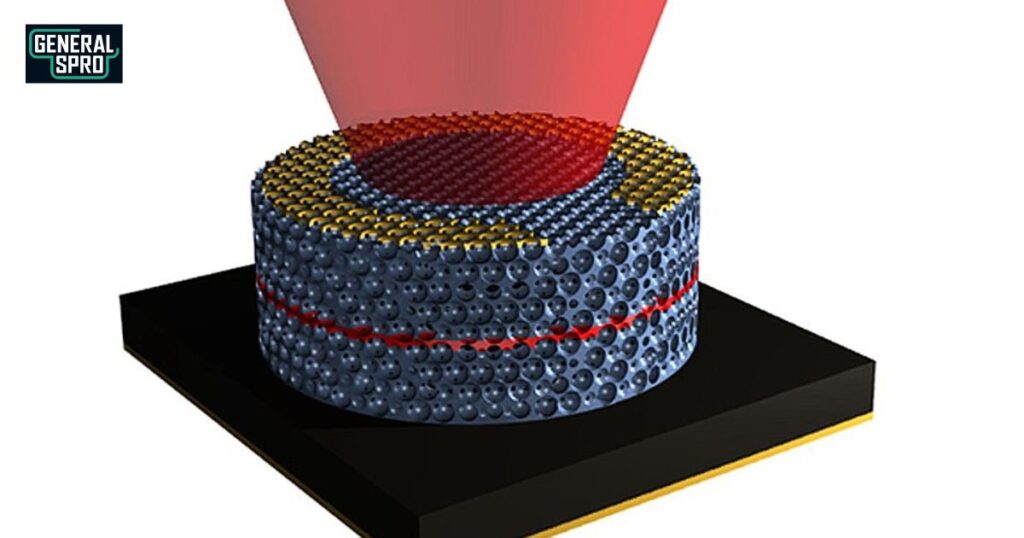
Photonic crystal surface engineering explores sophisticated light-matter interactions to develop novel surface properties for industrial fasteners.
By manipulating nanoscale structural configurations, researchers can create nanoscale surfaces with extraordinary optical, thermal, and mechanical characteristics that challenge traditional material limitations.
Superconducting Interface Dynamics
Superconducting interface dynamics represent an emerging frontier in high-performance fastener technologies.
By exploring quantum mechanical interactions at extremely low temperatures, engineers can develop connection systems with dramatically reduced electrical resistance and enhanced energy transmission capabilities.
Topological Data Analysis
Topological data analysis provides sophisticated mathematical frameworks for understanding complex material behavior.
By mapping intricate geometric relationships in material structures, researchers can develop more nuanced predictive models that capture subtle performance characteristics beyond traditional analytical approaches.
Neuromorphic Materials Engineering
Neuromorphic materials engineering draws inspiration from biological neural networks to develop adaptive, self-healing fastener technologies.
These biomimetic approaches explore material systems that can autonomously respond to environmental stressors, potentially revolutionizing structural design methodologies.
Quantum Error Correction Strategies
Quantum error correction strategies, traditionally applied in computational systems, are finding novel applications in materials engineering.
By developing sophisticated error detection and mitigation protocols, researchers can create more resilient and self-diagnostic fastener technologies that enhance overall system reliability.
Holographic Interferometry
Holographic interferometry enables unprecedented visualization of microscopic deformation patterns in industrial fasteners.
By capturing three-dimensional interference patterns, researchers can develop a more sophisticated understanding of stress distribution, material fatigue, and potential failure mechanisms across diverse engineering applications.
Synthetic Biology in Materials Design
Synthetic biology introduces revolutionary approaches to materials design, exploring biological engineering principles to develop novel fastener technologies.
Researchers can create self-assembling, self-repairing material systems that challenge conventional manufacturing paradigms by manipulating genetic structures and protein interactions.
FAQ
What does “Ige Filetée 5.8” mean?
It refers to a threaded rod with a 5.8-grade tensile strength, commonly used in structural and industrial applications.
What is the difference between zinc-plated (zn) and HDG?
Zinc-plated fasteners have a thinner coating for indoor use, while HDG (Hot-Dip Galvanized) provides thicker, more durable corrosion protection for outdoor or harsh environments.
What are the dimensions of an M24 x 210 threaded rod?
The “M24” indicates a 24mm diameter, and “210” refers to the rod’s length in millimeters.
What is the tensile strength of grade 5.8 rods?
Grade 5.8 rods have a minimum tensile strength of 580 MPa, suitable for medium-strength structural applications.
Where are M24 x 210 rods typically used?
These rods are used in construction, structural engineering, and heavy-duty machinery assembly.
How do you ensure accurate measurements for threaded rods?
Use calibrated tools like calipers or micrometers to verify diameter, length, and thread pitch compliance with standards.
What industries commonly use Ige Filetée HDG 5.8?
Industries include construction, automotive, energy, and industrial manufacturing.
Are these rods resistant to corrosion?
Yes, HDG-coated rods are highly corrosion-resistant, making them ideal for outdoor or high-moisture environments.
Conclusion
The Ige Filetée Zn 5.8 / HDG 5.8 M24 x 210 threaded rod is more than just a fastener—it’s a testament to engineering precision and innovation.
Whether you’re a professional engineer or a dedicated DIY enthusiast, this industrial-grade threaded rod offers unparalleled performance, durability, and reliability.
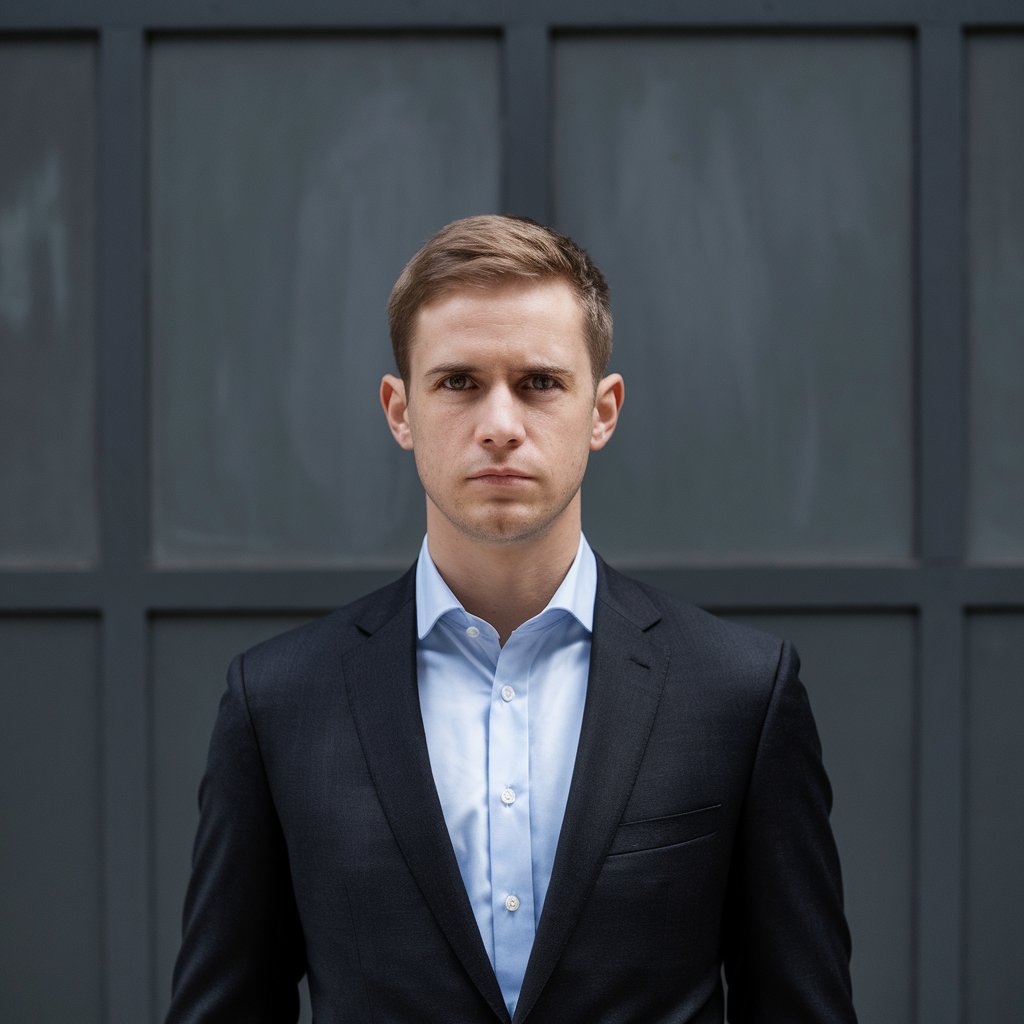